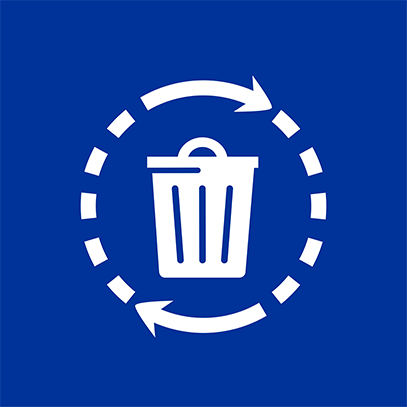
Verantwortungsbewusster Umgang mit Rohstoffen
In den Werken Lederdorn und Nyrsko der uvex sports group wurde ein Verfahren zum Entsorgen, Sortieren und Rückführen von Plastikabfällen eingeführt. Bernhard Preis, kaufmännischer Leiter uvex sports Lederdorn, und Stefan Schimpe, Logistik/Ausbildung uvex sports Lederdorn, über die Hintergründe des Projektes:
Wie ist die Idee entstanden, Abfälle bzw. Rohstoffe an die Industrie zurück zu führen?
Bernhard Preis: Beim Spritzgussverfahren fällt schon immer viel Ausschuss an. Aus der Belegschaft kam 2014 der Vorschlag, zu überlegen was wir mit den Kunststoffabfällen machen könnten. Professionelle Unterstützung haben wir dabei von einer Entsorgungs- und Recyclingfirma aus der Region erhalten. Es hat sich dann als sinnvoll herausgestellt, bei uvex sports Lederdorn ein Verfahren einzuführen, welches die Abfälle sortenrein trennt, bevor sie der Wiederverwertung zugeführt werden.
Wie sieht dieses Verfahren im Detail aus?
Stefan Schimpe: Unser Konzept für das Werk Lederdorn sah so aus, dass wir Sammelpunkte mit Containern zur Trennung der jeweiligen Abfälle eingeführt haben. Karten erklären ganz genau, was wo hineinkommt. So werden Kunststoffe, aber auch Produktanteile wie z. B. Helmschalen, geschreddert und wieder der Industrie zugeführt. Viele Abfälle können so als wertvoller Rohstoff wiederverwendet werden. Es bleibt natürlich auch ein Teil übrig, der nicht zweitverwertet werden kann, sondern entsorgt werden muss.
Wie hoch war der Aufwand, das System vor Ort einzuführen?
Bernhard Preis: Das System wurde von den Mitarbeitern nach einer Schulung und einigen Wochen der Umstellung sehr positiv und schnell aufgenommen. Es erinnert fast ein bisschen an die Mülltrennung zuhause. Weil sich das Konzept als erfolgreich erwiesen hat, haben wir es im Jahr 2016 auch in unserem Werk in Nyrsko eingeführt.
Stefan Schimpe: Dort fallen außerdem Abfälle wie Plattenmaterialien, Schäume, Kartonagen, Blech oder Textilien an, die über den gleichen Recyclingspezialisten entsorgt und recycelt werden können. Der Prozess hat sich auch aus ökonomischer Sicht ausgezahlt. Die Kosten für die professionelle Wiederaufbereitung bleiben hinter den Entsorgungskosten vor 2014 zurück – eine Win-Win-Situation für unsere Werke und die Umwelt.
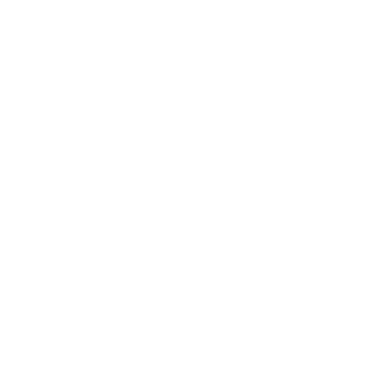
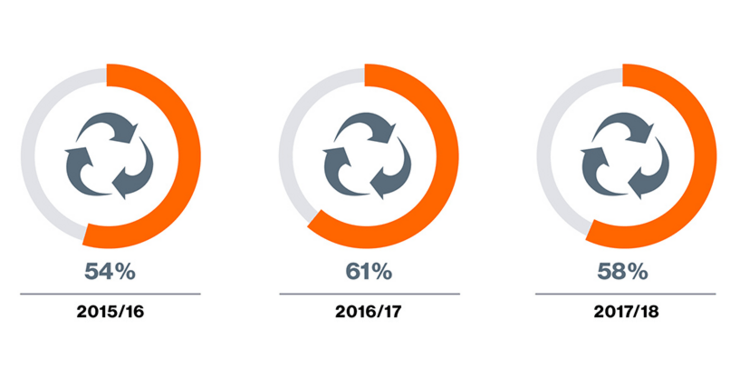
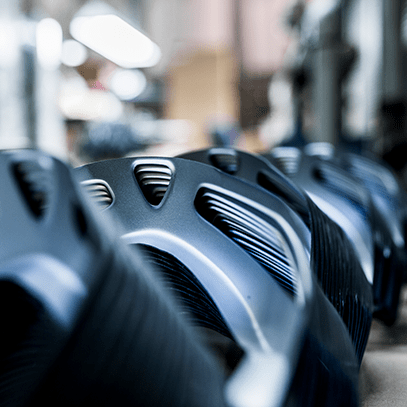
BSA Obernzell
Im Geschäftsjahr 2017/18 setzte der Produktionsstandort BSA (Obernzell) erstmalig erfolgreich ein neues Anlagenkonzept für das Schäumen von den dort produzierten Ski-, Rad- und Reithelme um. Der Ausbau des Maschinenparks, der sich durch Stückzahlsteigerungen ergibt, erfolgt durch diesen Maschinentypen und durch deren Einsatz wird pro neuer Maschine eine Einsparung von 20 bis 25 Prozent Energie, im Vergleich zu einer herkömmlichen Maschine realisiert. Eine Erweiterung des Maschinenparks und damit weitere Investitionen in die Technologie vor Ort sind in Planung.