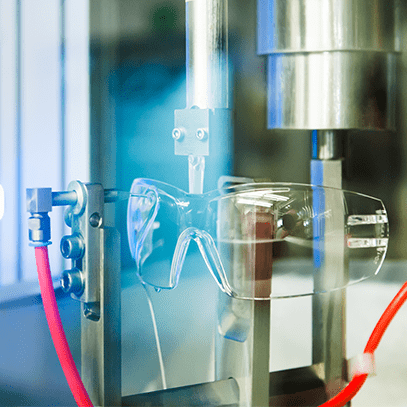
Austausch der zentralen Optidur durch innovative Flutzellen
Im Dezember 2019 wurde die zentrale Optidur zur Beschichtung von Brillenscheiben endgültig durch innovative Flutzellen ersetzt, dadurch können Energie und Lack eingespart und gleichzeitig eine bessere Performance im Beschichtungsprozess erreicht werden. Durch die kürzeren Rüstzeiten ist ein schnellerer Wechsel zwischen verschiedenen Modellen und Lacksystemen möglich. Gleichzeitig erhöht sich die erzielbare Qualität der Beschichtungen signifikant. Außerdem ist der Energieverbrauch der neuen Flutzellen trotz besserem Output und höherer Variabilität geringer als in der Optidur. Dadurch können im Jahr knapp 44.000 kWh Energie eingespart werden, was einem durchschnittlichen Jahresverbrauch von elf 4-Personen-Haushalten entspricht. Der Lösemitteleinsatz fällt ebenfalls geringer aus.
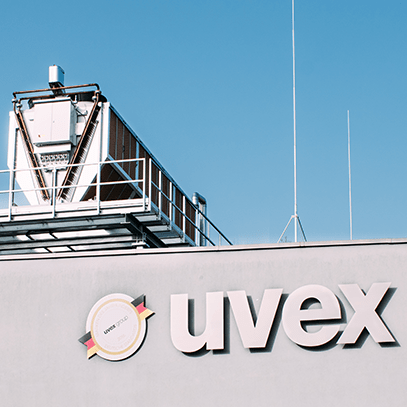
Installation eines adiabaten Freikühlers
Für die Schutzbrillen-Produktion ist eine stetige Kühlung der Spritzgussmaschinen notwendig. Durch Benetzung der Kühleroberfläche mit Wasser arbeitet der Freikühler bis zu einer Außentemperatur von 32 Grad Celsius. Oberhalb dieser Temperaturen wird energieintensive Kompressorkälte benötigt. In nächster Umgebung des Unternehmens befindet sich Wohnbebauung, weshalb Lärm ein wichtiges Thema darstellt. Durch modernste Ventilatortechnik kann in der Nacht mit etwas mehr Wasser und einer geringeren Ventilatordrehzahl somit die Lärmemission des Werkes unterhalb der gesetzlichen Grenzwerte gehalten werden. Durch die Installation des Freikühlers werden für die Kühlung aller Spritzgussmaschinen zukünftig 233.000 kWh pro Jahr eingespart. Dies entspricht dem durchschnittlichen Jahresverbrauch von 58 4-Personen-Haushalten.